Understanding Rotary Drills: Mechanisms and Uses
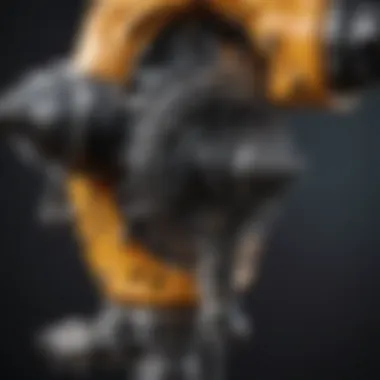
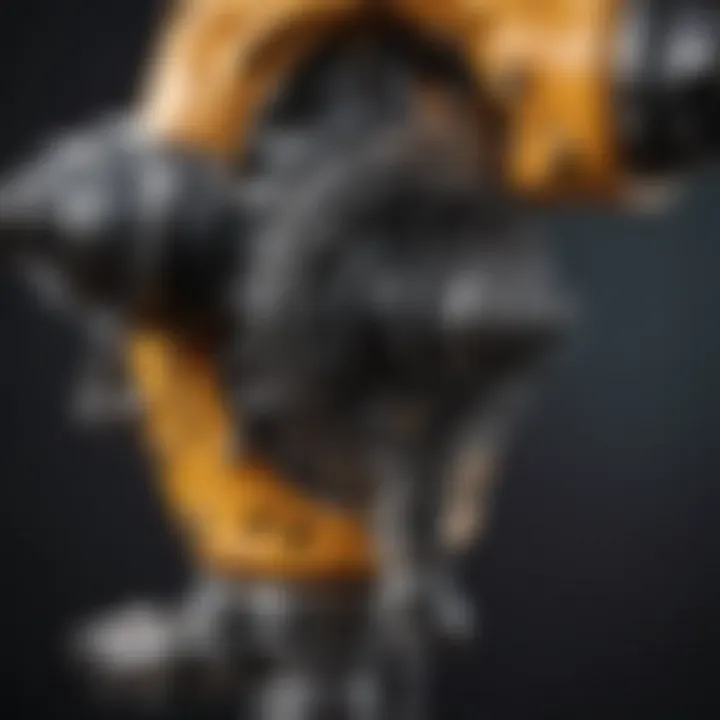
Intro
Rotary drills play a crucial role in various sectors of industry and daily life. Their importance stems from their versatile applications, ranging from construction to pest management. Understanding these machines allows us to appreciate their design, functions, and a broad range of uses. This article will explore the mechanisms that make rotary drills efficient, their benefical impact across different fields, and the latest advancements in drilliing technology. Additionally, we will delve into necessary safety precautions and maintenance best practices to ensure optimal performance.
Mechanisms of Rotary Drills
Basic Components
Rotary drills consist of several essential parts that work together to perform their tasks effectively. Key components include:
- Drill bit: This is the cutting tool that penetrates the material being drilled. The type of drill bit varies based on the application.
- Body or chassis: This is the main structure housing other components, providing stability and support.
- Power source: Electric engines or internal combustion engines are common power sources, determining the drill's capacity and efficiency.
- Feed mechanism: This allows the drill to apply pressure on the bit, enhancing its cutting effectiveness.
Operational Principles
The operational principle of rotary drills centers around their ability to rotate and apply pressure. When powered on, the drill bit rotates at high speeds. This rotation, combined with downward force, enables the bit to cut through various materials such as wood, concrete, rock, and more. The effectiveness of these drills stems from this simple yet powerful mechanism.
Applications Across Industries
Rotary drills find applications in multiple sectors, each leveraging their unique capabilities. Here are some notable examples:
Construction Industry
In construction, rotary drills are indispensable for creating holes for foundations, anchors, and utilities. Their efficiency significantly reduces time compared to manual drilling methods. The choice of drill bit determines the type of material it can adequately penetrate, allowing adaptability across various construction tasks.
Mining Sector
Mining employs rotary drills to extract valuable minerals and resources. These heavy-duty machines can bore through tough rock formations, enabling access to ores. Their role is not only limited to drilling but also extends to geological surveying where understanding the subsurface is essential.
Pest Management
In pest management, rotary drills assist in creating access points for chemical treatments or physical barriers. These drills allow for minimal disruption to the environment while effectively targeting pest infestations.
Technological Advancements in Rotary Drills
The evolution of technology enhances the capabilities of rotary drills significantly. New materials, such as high-speed steel and carbide-tipped bits, increase durability and performance. Furthermore, incorporation of electronics improves efficiency and user-friendliness.
"Understanding the advancements in drilling technology can lead to enhanced efficiency, safety, and effectiveness in various applications."
Safety Precautions and Maintenance
Ensuring safe and efficient operation of rotary drills involves ascertaining necessary safety measures:
- Always wear appropriate protective gear, including goggles and gloves.
- Ensure that all equipment is well maintained to prevent accidents.
- Always follow the manufacturer’s instructions for safe use.
Regular maintenance checks not only extend the life of the drill but also ensure that it functions safely. This includes checking the drill bits for wear, inspecting power sources, and ensuring proper lubrication of moving parts.
Foreword to Rotary Drills
Rotary drills play an essential role in various industries including construction, mining, and agriculture. Their importance is driven by their capacity to perform tasks efficiently and effectively. Employing rotary drills can significantly impact workflow and productivity. A deep understanding of rotary drills includes knowing their components, operation, and practical applications. This foundational knowledge is crucial for housewives and homeowners who may need to utilize these power tools for home improvement projects or maintenance tasks.
Definition and Overview
A rotary drill is a power tool that uses a rotating motion to cut into materials such as wood, metal, or concrete. There are many types of rotary drills, including electric, pneumatic, and hydraulic models. The efficiency of these tools lies in their ability to perform various drilling tasks swiftly. Knowledge of the types of rotary drills can help users choose the right tool for their needs.
Historical Background
The development of rotary drills has a long history, dating back to ancient times. The earliest drills were simple hand tools. However, the need for faster and more efficient methods in construction and mining led to innovations. In the 19th century, mechanical rotary drills emerged, paving the way for the advanced drilling technology we see today. The modern rotary drill has benefited from advancements in materials and engineering, enabling it to operate at higher speeds and with greater precision. This historical perspective adds significant weight to understanding the present-day uses and capabilities of rotary drills.
"The evolution of rotary drills from simple hand tools to complex machines reflects the demand for efficiency in various fields."
By grasping these concepts, readers will appreciate the complexities and capabilities of rotary drills, thus preparing them for the subsequent sections regarding mechanics, applications, and safety considerations.
Mechanics of Rotary Drills
Understanding the mechanics of rotary drills is crucial in appreciating their effectiveness and versatility across various applications. The functionality of a rotary drill is dictated by its components and operating principles. Ensuring that each part works efficiently contributes to the overall performance. Key elements such as the drill bit, motor, chucks, and gear mechanisms play integral roles. Their interactions dictate the drilling speed, power, and precision. These details are essential for users, whether they are professionals or casual users in home projects.
Key Components
Drill Bit
The drill bit is perhaps the most critical element of any rotary drill. It is the part that directly interacts with the material being drilled. The design of drill bits varies significantly based on their intended purpose, from masonry to metal drilling. A distinctive feature is the cutting edge pattern which can vary to suit different materials.
Drill bits made from high-speed steel are popular because they can withstand high temperatures generated during drilling. However, carbide-tipped options, while more expensive, offer greater durability and efficiency. Choosing the right drill bit ensures better results and less wear on the drill itself. This aspect makes it a central focus in any discussion regarding the mechanics of rotary drills.
Motor
The motor in a rotary drill provides the necessary power to turn the drill bit. Electric motors dominate in typical home drills, offering consistent speed and torque. The motor efficiency is key; more efficient motors consume less energy and can sustain longer periods of operation without overheating.
A unique feature of motors is how they can be adjusted to vary speed settings. This adjustability allows users to match speed to the material, improving performance. While powerful motors facilitate heavy-duty tasks, they can make the drill heavier, presenting challenges for prolonged use.
Chucks
Chucks hold the drill bit securely in place during operation, allowing users to swap bits conveniently. Key characteristics include the type and size of the chuck, which directly influence the types of drill bits that can be used. Keyless chucks offer ease of use, making bit changes faster and without tools. However, they might not provide the same grip as keyed chucks, which can sometimes lead to slipping during use.
In the context of rotary drills, having the right chuck ensures compatibility with various drill bits, making it an important aspect to consider. Chucks can also affect the drill's capability, particularly in heavy-duty applications where grip strength is vital.
Gear Mechanisms
Gear mechanisms are essential for manipulating the torque and speed of the rotary drill. They ensure that sufficient force is applied to the drill bit while controlling its rotational speed. High-gear configurations are often employed for speed, while low-gear settings provide more torque for demanding materials.
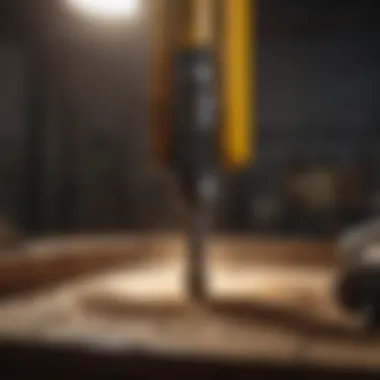
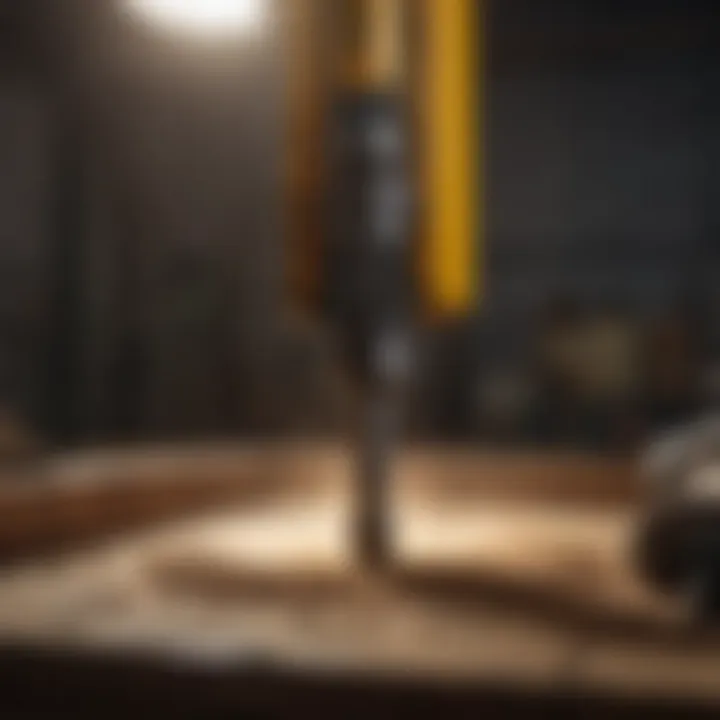
One key advantage of gear mechanisms is their ability to enhance the drill's versatility. Different gear settings can adapt the tool to various drilling needs, from delicate tasks to tougher applications. Nonetheless, the complexity of gear systems can also lead to maintenance challenges, requiring users to be mindful of wear and tear.
Operating Principles
Rotational Motion
Rotational motion is the foundation of how rotary drills function. The motor generates this motion, allowing the drill to spin the drill bit. This motion facilitates penetration into various materials. A critical characteristic that stands out is its continuity; uninterrupted rotation is needed for effective drilling. When smoothly operational, it significantly enhances drilling efficiency.
However, factors like excessive pressure can affect this motion, causing strain on the motor and potential overheating. Understanding the rotational dynamics can help users optimize drilling performances in different materials and scenarios.
Pressure Application
Pressure application is vital in achieving effective results with rotary drills. The applied pressure determines the rate at which the drill advances into the material. By managing this pressure, a user can control the depth and speed of drilling.
A unique advantage lies in the adaptability of pressure control. For example, softer materials require less pressure, while harder substances need increased force. This adaptability enhances the drill's efficiency and prolongs the lifespan of bits by reducing excessive wear.
Speed and Torque
Speed and torque are interrelated concepts crucial to rotary drill operation. Speed refers to the rate at which the drill bit spins, while torque is the rotational force exerted. Understanding when to prioritize speed or torque allows users to optimize their drilling strategy.
In general, lower speeds with high torque are beneficial for tougher materials, ensuring better penetration. Conversely, high speeds are preferable for softer materials, improving efficiency. This dynamic interplay of speed and torque underscores the importance of understanding the applications of rotary drills, ensuring users achieve the desired results.
Types of Rotary Drills
Understanding the different types of rotary drills is essential for selecting the right tool for specific tasks. Each type has unique features, operation methods, and benefits. This knowledge can help both professionals and home DIY enthusiasts make informed decisions, ensuring the right drill for the job.
Electric Rotary Drills
Electric rotary drills are likely the most commonly used drills in today’s market. Operating on electrical energy, they provide consistent power and speed that can be adjusted based on the task. This adaptability makes them suitable for a variety of applications, from small household tasks to construction sites.
Some key benefits of electric rotary drills include:
- Ease of Use: They are straightforward to operate, even for beginners, making them a popular choice among homeowners.
- Maintenance: Electric drills require less maintenance compared to other types. They have fewer moving parts that can wear out over time.
- Power Options: Many models offer battery or corded options, providing flexibility in work environments.
However, there are considerations to keep in mind. Electric drills are limited by cable lengths for corded versions, and battery life can be an issue for cordless units during prolonged use.
Pneumatic Rotary Drills
Pneumatic rotary drills rely on compressed air to operate. These drills are powerful and are often used in industrial and construction settings. Their design allows for durability and high performance, particularly when drilling through hard materials like concrete.
Benefits of pneumatic drills include:
- High Torque Output: This makes them ideal for heavy-duty applications.
- Lightweight: Despite their power, they tend to be lighter than electric counterparts, reducing user fatigue.
- Continuous Operation: As long as there is air supply, they can work without the risk of overheating.
Nonetheless, there are challenges. Pneumatic drills can require additional investments in air compressors. They may not be ideal for home use due to the need for a specialized air supply system.
Hydraulic Rotary Drills
Hydraulic rotary drills utilize hydraulic fluid to generate power. These drills are generally found in applications that require deep drilling, such as mining and well drilling. Their design provides exceptional power and stability during demanding tasks.
Key advantages of hydraulic rotary drills are:
- Exceptional Power: Capable of penetrating very hard materials thanks to their hydraulic force.
- Stability: They maintain consistent performance under extreme conditions, reducing the likelihood of equipment failure.
- Versatile Applications: Ideal for large-scale projects that necessitate deep holes, such as drilling for oil or geological studies.
However, their size and complexity can make hydraulic drills unsuitable for casual home use. Additionally, they typically require a trained operator to handle effectively.
Overall, selecting the appropriate type of rotary drill hinges on the specific needs of each project. Electric, pneumatic, and hydraulic drills serve distinct roles, with advantages that cater to different applications. Understanding these options allows for improved efficiency and effectiveness in drilling tasks.
Applications of Rotary Drills
Understanding the applications of rotary drills is essential to grasp their significance within various industries. Rotary drills serve as invaluable tools that enhance operational efficiency, increase productivity, and enable precise outcomes across diverse fields such as construction, mining, and pest management. Each application highlights specific features and benefits that cater to distinct requirements, showcasing the adaptability of rotary drills in real-world scenarios.
Construction Industry
Foundation Drilling
Foundation drilling is a critical aspect of construction that involves creating boreholes for building foundations. This process is fundamental for ensuring stability in structures, especially in areas with challenging soil conditions. The key characteristic of foundation drilling is its ability to penetrate deep into the ground, reaching suitable strata for support. This makes it a popular choice in constructions involving tall buildings or infrastructures like bridges and parking garages.
The unique feature of foundation drilling lies in its precision and adaptability to various soil types. By employing rotary drills, builders can achieve precise depths and diameters necessary for foundation specifications. The advantages of this technique include reduced time for construction, decreased labor costs, and a less disruptive process compared to traditional excavation methods. However, there are disadvantages, such as the potential for soil disturbance or contamination if not conducted properly.
Installation of Utilities
The installation of utilities often requires drilling for pipelines, electrical conduits, and telecommunications networks. This application is crucial for modern infrastructure development. The key characteristic here is the efficiency with which these drills can create pathways beneath roads or other structures. This minimizes the need for extensive surface disruption, making it a favorable option in densely populated or urban areas.
The unique feature of utility installation using rotary drills is its capability to navigate and work in confined spaces without damaging surrounding environments. Such a method offers advantages like reduced installation time and less inconvenience to the public. However, challenges can arise with identifying existing infrastructure or avoiding underground hazards, necessitating careful planning and surveying before drilling starts.
Mining and Resource Extraction
Drilling for Minerals
Drilling for minerals is a foundational activity in the mining industry, where rotary drills play a vital role. This process involves creating boreholes to locate and extract mineral deposits. The key characteristic of this type of drilling is its depth and accuracy in identifying mineral-rich areas. As such, it becomes a beneficial choice for mining operations aiming to optimize resource extraction.
A unique feature is the ability of rotary drills to operate under harsh conditions, such as rocky terrain or extreme weather. This attribute enhances exploration capabilities, facilitating access to valuable resources. Advantages include higher extraction rates and lower operational costs. It can have disadvantages, such as environmental impacts, including land degradation and potential groundwater contamination, if not managed correctly.
Geotechnical Applications
Geotechnical applications also rely heavily on rotary drills, with purposes ranging from soil testing to site investigations. These applications are paramount for ensuring the safety and suitability of construction projects. The key characteristic is their function in assessing soil and rock properties before any building begins, acting as a preventive measure.
The unique feature of geotechnical drilling is its dual benefit of providing essential data while simultaneously reducing risks associated with unforeseen subsurface conditions. The advantages are substantial, including informed decision-making and improved project outcomes. On the flip side, challenges may include the need for skilled personnel and potential project delays if conditions vary dramatically.
Pest Management Applications

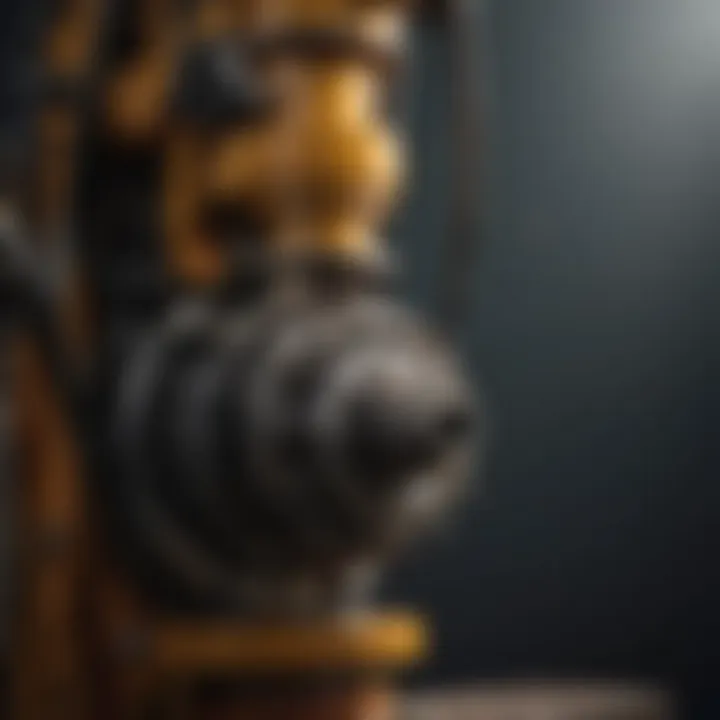
Targeted Wood Treatment
Targeted wood treatment is a specialized application where rotary drills are utilized to administer pest control solutions to wooden structures. Wood, being susceptible to pests, necessitates strategic approaches for treatment. The key characteristic here is the precision of delivering treatments directly to affected areas, which enhances the efficacy of pest management solutions.
The unique feature of this application is the minimal impact on surrounding wood, ensuring that only specific areas receive treatment. This method has clear advantages, including lower chemical usage and reduced environmental impact. Nevertheless, there are disadvantages, such as potential costs involved in specialized equipment and expert application.
Soil Applications for Pest Control
Soil applications for pest control involve using rotary drills to inject pest treatments directly into the soil, targeting burrowing insects or pests that reside underground. This approach is significant for maintaining healthy landscapes. The key characteristic is the depth and specificity with which treatments are applied, which allows for effective pest management.
The unique feature is the ability to reach pests hidden beneath the surface without disturbing the overall soil structure. Advantages include targeted treatment that minimizes chemical exposure to non-target organisms. Disadvantages might relate to the potential for uneven distribution if not executed carefully, leading to less effective pest control outcomes.
In summary, each application of rotary drills highlights their versatility across various industries. The efficiency, precision, and adaptability of these tools not only enhance productivity but also significantly contribute to the effectiveness of tasks in construction, mining, and pest management.
Advantages of Rotary Drills
The significance of rotary drills lies in their many advantages across various applications. These tools have proven essential in enhancing productivity, simplifying complex tasks, and ensuring high standards of work. In this section, we will delve into the key benefits of rotary drills, which contribute to their widespread use in multiple sectors.
Efficiency and Speed
Rotary drills are known for their ability to perform tasks quickly. This efficiency saves time, especially in large projects. The mechanism of rotary drills allows for continuous operation with minimal downtime. Due to their high RPM (rotations per minute), they can penetrate various materials faster than traditional drilling methods.
Moreover, electric rotary drills can maintain consistent speeds, adapting to the material they are drilling into. As a result, they reduce the likelihood of overheating and wear. This aspect is particularly important for contractors and home improvement enthusiasts, enabling them to complete projects in shorter timeframes.
Precision and Control
Precision is another vital advantage of rotary drills. The design of the drill bits and the ability to adjust speed contribute to accurate drilling. This accuracy becomes crucial in tasks like foundation drilling in construction, where exact measurements are required.
Operators can manage the depth of the drill effectively. This control minimizes errors and reduces waste, ensuring a better fit for fixtures. Additionally, many rotary models feature built-in guides that enhance stability, allowing for flawless execution in complex projects.
Versatility
Versatility is an important attribute of rotary drills. They can be used for various applications, not just limited to drilling. Rotary drills can also assist in tasks such as sanding, grinding, and polishing with the right attachments. This multi-functionality makes them invaluable in workshops, homes, and job sites.
From construction and plumbing to pest management, these tools adapt to meet many needs. For example, in landscaping, rotary drills can help create holes for planting trees or installing fencing. Their diverse capabilities make rotary drills a wise investment for homeowners.
"Investing in a rotary drill is about efficiency, precision, and versatility. It's a decision that pays dividends in productivity and quality."
In summary, the advantages of rotary drills are significant. Their efficiency and speed enhance productivity, while their precision and control improve overall quality. The versatility of these tools makes them essential for various tasks, ultimately making them a valuable addition to any home or professional workspace.
Technological Advancements in Rotary Drills
Technological advancements play a critical role in the evolution of rotary drills. These improvements enhance operational efficiency and safety, adapting to the increasing demands of various industries. As the functionalities of rotary drills progress, new technologies not only streamline drilling processes but also boost productivity.
Key Benefits of Technological Advancements:
- Increased Efficiency: Modern rotary drills now operate at higher speeds while maintaining precision. This improvement reduces the time needed to complete drilling tasks, ultimately leading to greater productivity.
- Enhanced Safety Features: Latest designs incorporate advanced safety protocols that protect users from accidents. Features like automatic shut-off mechanisms and improved user interfaces make drilling safer.
- Versatility in Applications: New technologies allow rotary drills to be adaptable for various applications, ranging from construction to pest management. This gives professionals more options based on their specific needs.
Advancements also promote sustainable practices in drilling operations. The introduction of smart technologies encourages energy-efficient drilling, minimize waste, and reduces environmental impact.
Smart Drilling Technology
Smart drilling technology represents a significant leap toward optimizing the drilling process. At its core, this technology utilizes sensors and connectivity to provide real-time data throughout drilling operations.
With this data, operators can make informed decisions, adjusting parameters for optimal performance. For instance, if sensors detect an obstacle beneath the surface, adjustments can be made quickly to avoid damage. This adaptability not only improves efficiency but also extends the lifespan of the equipment.
Moreover, smart drilling systems can integrate with software platforms for analyzing collected data. The insights gained from this analysis allow for better planning and resource allocation. This is particularly useful for long-term projects where precise calculations are essential.
Use of Artificial Intelligence
The implementation of artificial intelligence in rotary drills has revolutionized the drilling landscape. AI algorithms can analyze historic data, predict future outcomes, and optimize drilling methods. This predictive capability is essential in minimizing risks and improving overall effectiveness.
For example, AI systems can determine the best drilling patterns or identify when a mechanical failure might occur. This not only avoids potential downtime but also enhances safety by preventing hazardous situations.
In addition, AI-driven analytics can minimize human error during operations. By automating repetitive tasks, these systems free operators to focus on more complex actions, improving overall work quality. AI also promotes continuous learning as it evolves with every completed project, ensuring that the technology remains relevant and effective.
"The integration of artificial intelligence not only enhances operational efficiency but also provides valuable insights into equipment performance, leading to timely interventions and better planning."
Overall, the advancements in smart technologies and artificial intelligence represent a significant step forward in rotary drill capabilities. These innovations support workers while improving productivity and safety in various applications.
Safety Considerations
Safety is a critical aspect of any operation involving rotary drills. Understanding how to operate these machines safely can prevent accidents and minimize risks to both operators and bystanders. Awareness of safety measures should be embedded into every phase of using rotary drills, from preparation to execution. While rotary drills are powerful tools that enhance productivity, improper use can lead to severe injury or even fatalities.
Personal Protective Equipment
Personal Protective Equipment (PPE) is essential when working with rotary drills. This equipment acts as a barrier against potential hazards, helping to mitigate risks in various environments. The following items are commonly recommended for rotary drilling tasks:
- Safety Goggles: Protect the eyes from debris that may fly off while drilling.
- Ear Protection: Rotary drills can be quite loud, leading to potential hearing damage; earplugs or earmuffs are necessary.
- Gloves: These can protect hands from sharp objects and prevent fatigue during prolonged use.
- Steel-toed Boots: These provide necessary foot protection from heavy falling equipment.
- Hard Hats: Essential in construction sites to protect against falling objects.
Using PPE correctly does not solely depend on having the right gear but also on ensuring that it fits well and is maintained in good condition. By complying with safety regulations regarding PPE, operators can create a safer working environment.
Operational Safety Practices
In addition to PPE, implementing operational safety practices is crucial when utilizing rotary drills. Such practices include:
- Training and Certification: Operators should receive proper training on equipment use, ensuring they understand its mechanics.
- Pre-Operational Checks: These checks involve inspecting the drill for any wear, damage, or missing parts before use.
- Proper Technique: Operators should follow correct techniques for drilling, which includes maintaining a steady speed and applying consistent pressure.
- Work Area Awareness: Keeping the work area clear of unnecessary personnel and ensuring all participants are aware of the operation going on helps reduce risks.
- Emergency Protocols: Establishing and communicating emergency procedures is vital. This includes knowing how to quickly shut down the drill in case of a malfunction.
By focusing on these operational practices, the risk of accidents can be minimized, making rotary drilling a more secure activity for everyone involved.
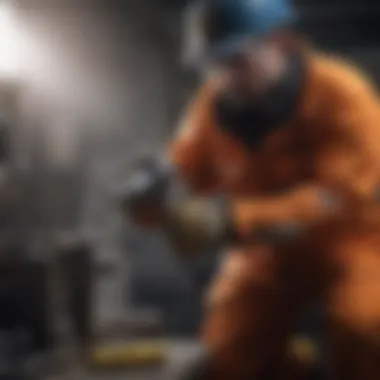
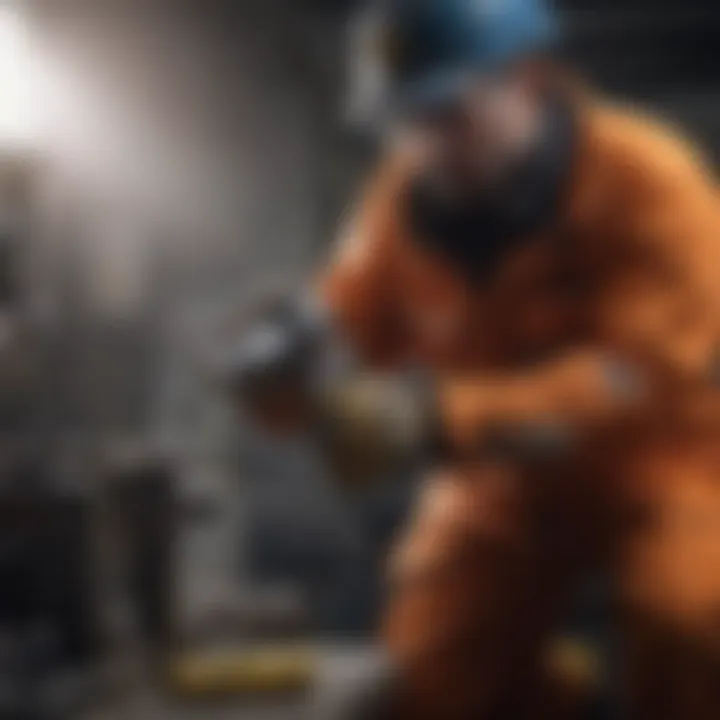
"Adhering to safety protocols is not just a legal requirement; it’s a moral obligation to ensure all workers go home safe each day." - Anonymous
Maintenance of Rotary Drills
The maintenance of rotary drills is a crucial aspect of ensuring their operational efficiency and longevity. Proper maintenance can greatly extend the lifespan of a rotary drill, reduce the likelihood of unexpected failures, and improve overall performance. Regular upkeep is not just about keeping the equipment running; it also plays a key role in safety and productivity on the job site. Neglecting maintenance can result in costly repairs and downtime, which is detrimental for both home projects and professional tasks. Understanding the important elements of maintenance can empower users to take actionable steps in keeping their drills in optimal condition.
Regular Inspection
Regular inspection is a fundamental maintenance practice that involves systematically checking the drill for any signs of wear, damage, or malfunction. This includes evaluating the drill bit, motor, and other critical components. A routine inspection should ideally take place before each use and include the following checks:
- Visual Inspection: Look for cracks, deformities or any wear on the drill bit and casing.
- Functionality Check: Ensure that all moving parts are functioning properly and efficiently.
- Electrical Connections: For electric rotary drills, inspect the power cord and plug for damage.
- Performance Assessment: Note any changes in performance during use that could indicate underlying issues.
By conducting these inspections, users can identify potential problems early on, which can prevent more significant issues and costly repairs later. Moreover, keeping a log of inspections can assist in tracking the drill's condition over time, providing valuable data for future maintenance.
Lubrication and Cleaning
Lubrication and cleaning are essential activities that aid in smoothing the operation of rotary drills and prolonging their lifespan. Lubricating moving parts reduces friction and heat buildup, which can cause premature wear. Cleaning helps prevent the buildup of debris and dust that could impede the drill's performance.
- Lubrication should be done according to the manufacturer's guidelines, focusing on parts that generate heat during operation. Common points to lubricate include:
- Cleaning should involve:
- The chuck to ensure smooth operation of the drill bit.
- Gears and bearings, which require periodic application of appropriate lubricants.
- Wiping down the exterior with a damp cloth to remove dust and dirt after use.
- Clearing the drill's internal components of any accumulated debris which can affect performance.
It is adviceable to use specialized cleaning solutions recommended for rotary drills, as common household cleaners might cause damage.
Regular lubrication and cleaning prevent many operational issues, helping maintain the integrity of the drill and enhancing its performance.
In summary, effective maintenance involving regular inspections, proper lubrication, and diligent cleaning ensures that rotary drills function efficiently and safely. Taking the time to address these aspects not only safeguards the tool but also enhances project outcomes, making it a worthwhile investment for homeowners and professionals alike.
Challenges in Rotary Drilling
The discussion of rotary drills must include the challenges they face in modern applications. Understanding these challenges is critical for both producers and users of rotary drills. The effectiveness of these tools can be significantly impacted by various factors, making it essential for users to navigate them thoughtfully. Addressing these issues enhances the longevity and efficiency of drills, ultimately affecting their overall performance in various environments.
Environmental Factors
Environmental factors present considerable challenges when using rotary drills. The presence of water, soil composition, and weather conditions can hinder drilling operations. For instance, drilling in wet soil can cause mud and debris to clog the drill bit, leading to equipment malfunction. Furthermore, adverse weather conditions, like extreme heat or cold, can affect the performance of the machinery and working conditions.
- Soil Type: Different soil types can greatly impact drilling efficiency. For instance, rocky terrain requires more robust drill bits and higher torque settings.
- Groundwater Issues: Encountering groundwater unexpectedly can complicate drilling and requires contingency plans for managing water ingress.
- Environmental Regulations: Compliance with environmental regulations is mandatory. Users must ensure their drilling methods do not harm local ecosystems or violate legal requirements.
Mitigating these environmental factors often demands thoughtful planning and investment in appropriate technology, which can increase overall costs. However, the investments are usually justified by the savings gained through improved efficiency and reduced downtime.
Material Limitations
Material limitations impose significant constraints on the types of projects feasible with rotary drills. Each material has unique challenges related to hardness, density, and chemical composition that can affect drilling methods and tool durability.
- Material Hardness: Harder materials necessitate specialized drill bits, increasing costs and reducing adaptability.
- Wear and Tear: The wear rate of drill bits can vary significantly based on the rock or material being drilled. Frequent replacements lead to more downtime and increased operational costs.
- Chemical Properties: Certain materials may react adversely with common drilling fluids or lubricants, which affects performance and can create additional safety concerns.
To address material limitations effectively, users often need to conduct comprehensive site assessments and possibly invest in custom solutions or more advanced technology. This foresight can enhance the efficiency of the drilling application while minimizing unexpected breakdowns.
"Understanding these challenges is crucial for the successful and efficient implementation of rotary drilling operations."
Navigating the challenges in rotary drilling takes experience and understanding. The interplay of environmental factors and material limitations is complex, yet crucial for effective drilling. Engaging in careful planning can yield better results, ensuring the longevity of equipment and success in various applications.
Future Trends in Rotary Drills
As industries evolve, understanding the future trends in rotary drills becomes crucial. These trends are informed by shifts in technology, environmental concerns, and user demands. The significance of these trends lies in their potential to enhance operational efficiency, reduce environmental impact, and improve user experience. A look into the future illustrates various exciting developments that may reshape how rotary drills function across multiple sectors.
Sustainability Initiatives
Sustainability is increasingly becoming a priority across various industries. Rotary drill manufacturers are beginning to adopt practices that minimize waste and reduce emissions. One of the aspects of these sustainability initiatives involves using materials that are less harmful to the environment. This includes the production of drill bits made from recycled metals and plastics. Moreover, companies are designin their products to be more energy-efficient, thus lowering overall power consumption.
Some important elements of sustainability in rotary drilling include:
- Eco-friendly Materials: Incorporation of sustainable materials in production.
- Energy Efficiency: Implementation of designs that consume less electricity.
- Waste Reduction: Enhancing the lifespan of equipment to minimize the frequency of replacements.
These initiatives not only benefit the environment but can also offer cost savings in the long run. Companies that prioritize sustainability may find increased approval from eco-conscious consumers, providing an avenue for market expansion.
Emerging Technologies
Emerging technologies present a new horizon for rotary drills, promising improvements in functionality and performance. Innovations such as artificial intelligence and smart sensors are starting to find their way into modern rotary drills, enabling real-time monitoring and adjustments during operation. This technology allows for a more precise drilling process, directly impacting accuracy and efficiency.
Key emerging technologies to consider include:
- AI Integration: Machine learning algorithms that optimize drilling parameters.
- Smart Sensors: Sensors to monitor temperature, pressure, and wear in real time.
- Automation: Drones and robotics that assist in drilling tasks, especially in hard-to-reach areas.
The impact of these advancements can lead to safer working conditions, enhanced productivity, and lower operational costs. By embracing these technologies, firms may position themselves as leaders in innovation, further driving industry standards upward.
The future of rotary drills lies in sustainability and technology. As companies adapt, they need to stay proactive in integrating these elements.
Ending
The conclusion of this article holds significant importance as it encapsulates the essence of rotary drills and their roles across various sectors. As discussed throughout the previous sections, rotary drills are not merely tools; they embody precision, efficiency, and versatility. By summarizing the key points, readers can better appreciate how these machines impact construction, mining, and pest management. It is crucial to understand that the effectiveness of rotary drills hinges on a combination of their mechanical design, advancements in technology, and adherence to safety practices.
Summary of Key Points
In this article, we examined various aspects of rotary drills, highlighting the following key points:
- Mechanics and Components: Rotary drills consist of essential elements such as the drill bit, motors, and gear mechanisms that facilitate their operation. Understanding these can help in making informed choices when selecting a drill.
- Types of Rotary Drills: Different types of rotary drills—including electric, pneumatic, and hydraulic—serve distinct purposes based on the operational requirements and environmental factors of the job.
- Applications: The applications in construction, mining, and pest management showcase the versatility of rotary drills, making them indispensable tools in these industries.
- Safety and Maintenance: Focusing on personal protective equipment and safety practices prolongs the life of these tools, ensuring the safety of operators.
- Future Trends: Embracing sustainability initiatives and emerging technologies can enhance the efficiency and environmental friendliness of rotary drilling processes.
Final Thoughts
In closing, rotary drills play a pivotal role in many fields. Their evolution has been marked by technological advancements that have substantially increased their efficiency and capabilities. As house owners and housewives engage in DIY tasks or maintenance jobs, understanding rotary drills can enable them to make better decisions regarding equipment selection and maintenance. By investing in quality rotary drills and adhering to recommended practices, users can optimize their performance and ensure safety. Comprehensive knowledge about rotary drills not only enhances practical skills but also fosters a greater appreciation for these engineering marvels.
"Knowledge is power, and in the world of tools, understanding your equipment leads to better results."
For more information about rotary drills and their applications, consider exploring resources like Wikipedia or Britannica.